With fuel and electricity prices increasing, now is a good time to investigate the potential of combined heat and power for reducing the cost of heating and hot water, says Andy Whitehouse
Combined heat and Power (CHP) is not a new concept in the UK but with fuel and electricity costs on the increase, this technology is currently experiencing somewhat of a revival thanks to its ability to generate electricity as well as heat. In short, a gasfired combined heat and power (CHP) 'module' offers a more efficient way to generate heat and electrical power, compared to conventional methods.
A typical CHP module consists of a gas engine, a generator and a heat exchanger system. The gas engine drives the generator to produce threephase electrical power, which feeds in to the main low voltage distribution system where it can be used locally or exported to the national grid (although there is no benefit for exporting electricity as CHP is not currently recognised by the Feed In Tariff).
Heat is produced as a by-product of the power generated, which in a conventional power station would be wasted. However, the heat generated by a typical CHP module is used to generate hot water via the integral heat exchangers. This hot water may be used for space heating, process heating or heating of domestic hot water. When hot water is not required immediately, it can be kept in a suitable storage vessel for later use (see schematic diagram).
The important point to make where CHP is concerned is that one size does not fit every application. It is vital to assess the viability of each individual project in order to determine if CHP is the most suitable technology for the job.
For starters, when embarking on a consultation project, my own company always requests around 12 months' worth of energy data - gas and electricity usage - from the customer. In addition to this, we also ask for details of the price per kW hour that people have been paying for those services so we can make a thorough assessment of a building's requirements and calculate payback timescales using a bespoke software package we've developed.
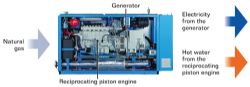
Another important benchmark we look for when assessing the viability of a site for CHP is a minimum of around 5,000 running hours per year. This is for the simple reason that, like all engines, a CHP module needs to warm up properly to operate at maximum efficiency.
Stopping and starting the engine within a CHP module is not advisable and can have a negative impact on the life of the technology over a period of time. Incorrect specification can therefore result in false economy for investors so, on occasions where the minimum running hours cannot be met, we always advise customers to consider other alternatives.
Running time important
Ideally, individual CHP modules need to be running for more than 15 - 16 running hours per day to ensure best performance and protect the life of the engine. It's also useful to take running time into consideration when calculating estimated payback figures too - and this is something that can also be done ahead of any installation taking place.
If calculations look positive, the next stage is to assess the correct size of CHP module required, taking into consideration what each module would be expected to contribute to electricity generation and the heating load of a building.
Fitting oversized units can lead to the production of too much heat for a building, meaning some of this has to be 'dumped' - thus reducing the total efficiency of the system. So getting this right is essential.
At this point it is always a good idea to arrange an onsite meeting between the CHP manufacturer/supplier and the customer. It pays to check seemingly obvious things, like the fact a plant room has enough space to accommodate CHP modules, as well as checking what flue
arrangements are required too.
Another golden rule of CHP specification is that CHP modules should always be installed in conjunction with boilers for back-up and peak demand requirements. CHP systems should be sized according to a building's thermal base load to ensure maximum efficiency.
However, whilst CHP can meet this base load requirement most of the time, high efficiency boilers are needed to satisfy a building's peak heating load - such as during colder winter months - as CHP alone would not provide the most efficient solution.
Once installed, it is vital to take care of the long term 'health' of any CHP the system. At Buderus we don't sell CHP without customers first agreeing to have the protection of a service contract in place. This is for the simple reason that investing in CHP without being prepared to safeguard the long term running of the system is a huge false economy for investors.
If CHP units are not correctly maintained there is a risk of the engine within the module breaking down in years to come. When that happens, rebuilding the engine comes with a large cost attached and we often come across older installations that are no longer running simply because it was cheaper for the owner to switch them off as opposed to having them repaired in the end.
Problems like this are easily avoided. Within Buderus' service contract the engine is replaced after 44,000 running hours or approximately 5 years, to help maintain the life of the product and achieve optimum performance. So with due care and attention, there is no reason why CHP should fail to deliver heat and electricity as efficiently as possible (in partnership with a back-up boiler) for many years to come.
// The author is industrial and commercial technology consultant for Buderus //