The ventilation industry, in particular the ducting and damper manufacturers, have been at the forefront of CE Marking when it comes to fire protection.
In July 2013 it became a legal requirement under The Construction Products Regulation (CPR) for many life safety products such as fire rated ductwork systems and fire dampers to be CE Marked.
To comply, products must be fixed with a CE Mark after undergoing extensive independent third party testing. This includes fire resistance, environmental and durability testing according to the latest European Standards. In addition, continuous factory production controls and external auditing must also be in place.
This law applies to any construction product covered by a harmonised European standard (hEN). Any product which falls under a hEN but is not CE Marked can no longer be supplied or installed in the UK or the rest of Europe.
This challenge has been met by many of the leading ventilation industry manufacturers.
However, the fire protection of plastic ventilation ducting poses a much greater challenge than that posed by metal ducting.
Fire stop products capable of fire protecting plastic vent ducting should be tested to BS EN 1366-3 Standard. Such products are referred to as Penetration Seal Systems and fall under ETAG 026. They are typically intumescent based systems that expand in a fire situation to crush and seal off the vent duct and prevent fire spread.
This European fire testing, designed to replicate a flashover fire, is extremely onerous and aggressive with actual furnace temperatures capable of exceeding 500°C within the first minute. Clearly this poses a significant problem to thin plastic ducting which can typically start to melt within seconds of the test starting and subsequently fail in under a minute.
Any fire stop product must be capable of rapid expansion to ensure quick closure of the duct. A failure would be deemed to have occurred if any of the following is observed on the non-fire side:
Continuous flaming
Ignition of a cotton pad when applied to any hot spots
Gap gauge failure if a gap of more than 25mm is formed by slumping or burning through of the duct
Temperature on the non-fire side exceeding 180ºC + ambient
With a number of potential failures this is a significant challenge for a fire stop product, especially when you consider that the above must be maintained for up to 120 minutes with a fire raging at over 1000°C, possibly only 10cm away on the other side of a plasterboard wall.
There have been some common misconceptions in the construction industry surrounding how firestop products are tested and what should be deemed acceptable for plastic ventilation duct applications:
1 A fire stop product tested on thicker plastic must be OK for use on thinner plastic?
Wrong. Typically thicker plastics of even only 3-4mm in thickness can resist fire attack for several minutes giving a fire stop product more time to react in a fire. Most common PVC vent ducting is only around 1.5mm thick and can last less than a minute under fire attack.
A product tested on thicker plastic is no guarantee that it will work on thin plastic ducting as it may not react sufficiently quickly to perform. Specific evidence must be provided of testing carried out on the exact thickness of plastic to ensure fitness for purpose.
2 Testing of plastic pipes can be used as evidence for plastic vent ducting?
Wrong. Many plastic services, especially pipes, were tested with one or both ends capped off or closed in a fire test. This was typically done to replicate a continuous run of pipe and assumed the pipe was not ventilated.
Ventilated systems including ventilation ducting must be tested uncapped/uncapped with both ends left open to replicate the intended end use as detailed in BS EN 1366-3: 2009.
This makes the fire test significantly more aggressive as it gives the fire an unobstructed passage into the duct to replicate the situation in reality. Some products tested capped have been proven not to perform when tested uncapped/uncapped. Therefore any product used on plastic ventilation ducting must have been tested with both ends left open or uncapped /uncapped.
It is for the above reasons that many manufacturers continue to promote products under the old BS 476 test standards or do not test the product fully according to the requirements of EN 1366-3, as the new standard is simply too onerous for them to pass, ‘buyer beware’ still rings true.
Choosing a CE Marked fire stop product not only ensures that the product has been tested, manufactured and audited under strict controls, but also that the product is “fit for purpose”.
The range of Firefly 109 Vent Duct Fire Sleeves manufactured by TENMAT are the only penetration seal systems that are CE Marked approved specifically for use on PVC ventilation ducting. The products have been full scale fire tested for up to 120 minutes to BS EN 1366-3 with all ducting tested “Uncapped/Uncapped” and are additionally third party assessed.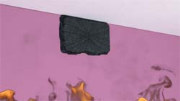
The Firefly 109 Vent Duct Fire Sleeves, which form part of TENMAT’s Queen’s Award winning range of fire protection can be specified, supplied, installed and approved with confidence, safe in the knowledge that the product will actually perform as required in a fire situation.
For further details please contact Chris Thompson - product manager, 0161 955 2478 or email chris.thompson@tenmat.com
The images show:
TENMAT Vent Duct Fire Sleeve installed on duct prior to fitting in wall
TENMAT Vent Duct Fire Sleeve expanded and sealed in event of a fire
Cross section of wall in event of a fire
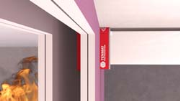